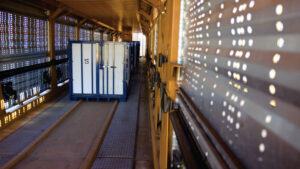
SOUTHFIELD, Mich. — A Detroit-area company aims to use its patented shipping containers to put loads of auto parts into multilevel railcars that otherwise would return empty to assembly plants.
Pro-Tech Group, which has designed containers to fit within the confines of auto racks that carry finished vehicles, has successfully completed pilot runs carrying pallets of wheel rims from California to Dearborn, Mich.
“The benefit of this process is to eliminate the 66,000 railcars that come back empty” each year, Pro-Tech CEO Earle B. Higgins tells Trains News Wire.
Higgins would not disclose which railroads handled the test loads for an unnamed automaker. But a video on the company’s website shows a forklift loading containers onto an auto rack via a Union Pacific ramp.
The 22-inch wheels are imported in California, sent to a manufacturer in the Golden State, and then distributed to automakers.
Each of Pro-Tech’s containers holds two pallets of wheels. A bilevel auto rack can accommodate up to 18 of the containers. A trilevel auto rack, which is in greater supply than bilevels used to transport SUVs and other larger vehicles, also can handle the containers, but only on the lower two levels, says Higgins, who spent 27 years working in logistics at Chrysler and is familiar with the automotive supply chain.
What’s the size of the potential market for using multilevel equipment?
“I think it’s huge,” Higgins says. “Anytime you have 66,000 auto racks moving empty, there’s opportunities to grow. And the good thing is we can build our containers at the size of the commodities we move.”
The containers can be built to handle loads of different sizes. Higgins says the boxes could carry any kind of freight — not just auto parts — so long as the loads are not hazardous materials or food products.
When empty, the containers can be folded flat, with 10 containers taking up the space of one assembled box. They are designed to return to origin via intermodal trains, with 60 to 80 of the folded boxes able to hitch a ride on an intermodal car, Higgins says.
Pro-Tech is currently in negotiations with Class I railroads and automakers about launching revenue service.
Railroads stand to gain from new revenue moves of equipment that normally would move empty, while automakers can shave costs and their carbon footprint by using rail, Higgins says.
“This, we believe, is the start of something,” Higgins says of the test runs.
Some industry observers aren’t so sure, citing the non-standard size of the containers and the complexity that adds to the supply chain, from trucking loads to an auto ramp to collapsing the boxes and transporting them empty back to origin.
“It always sounds good in theory to utilize the empty backhaul, but I see a lot of cost in all these steps,” says intermodal analyst Larry Gross.
Says another analyst: “It’s an interesting niche concept … but these types of systems are very complicated because the parts don’t often come from the consuming markets where the cars are destined.”
Higgins says Pro-Tech has done due diligence on overall costs and has approached six of the seven Class I railroads, as well as TTX, which manages the pool of multilevel equipment.
From his days at Chrysler, Higgins was aware of rail industry efforts to minimize empty miles that auto racks run off every year. “They wanted to know why they didn’t think of it,” Higgins says of his containers, which received a patent in 2016.